Revolutionizing Construction and Manufacturing with Advanced Volumetric Concrete Plant Technology
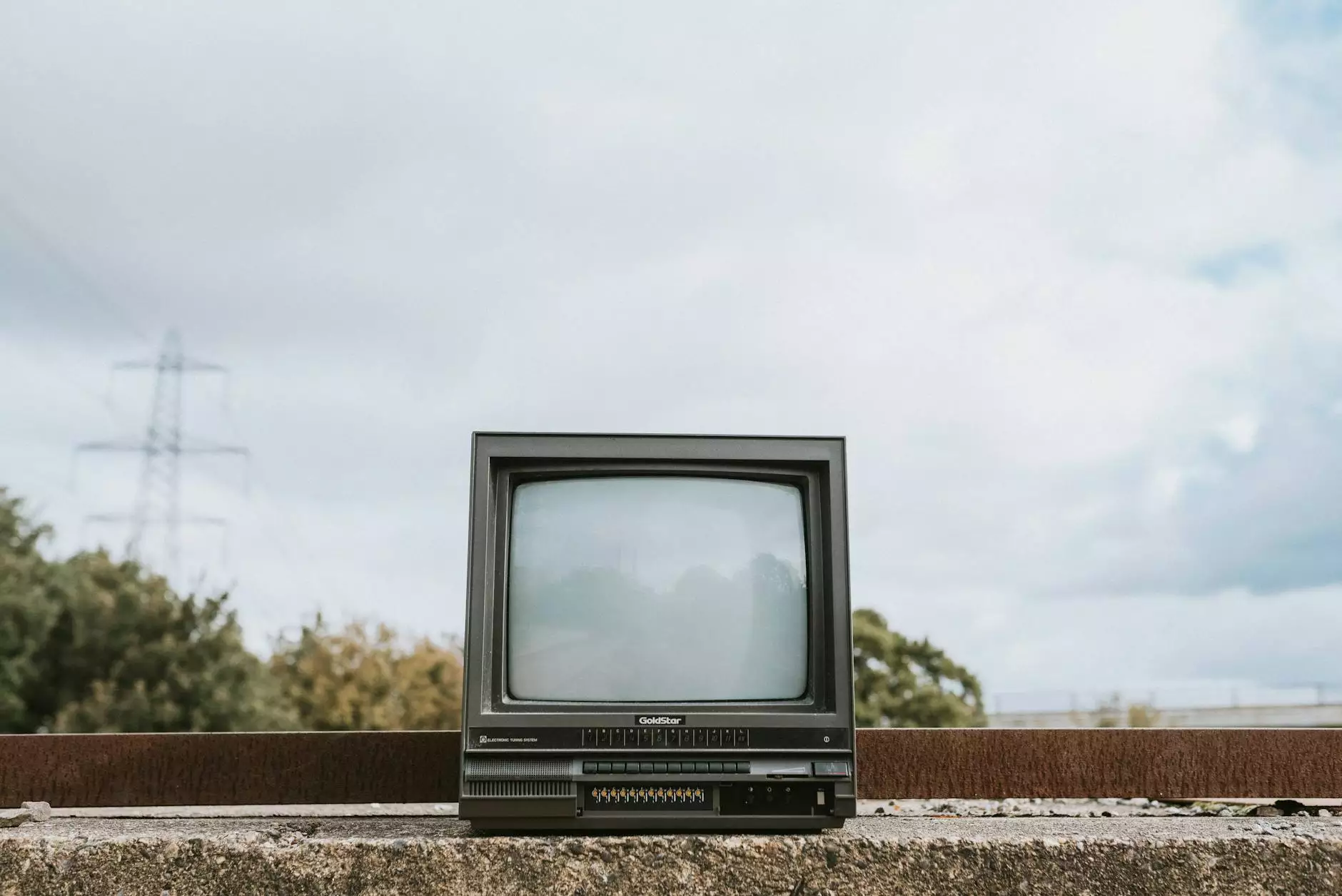
The construction and manufacturing sectors are constantly evolving, driven by technological innovation and the pursuit of efficiency. Among the most groundbreaking advancements in recent years is the development of volumetric concrete plants. These systems are redefining how concrete is produced, offering unparalleled flexibility, precision, and sustainability. As an industry leader, Polygonmach is at the forefront of manufacturing innovative solutions, integrating electronics and 3D printing technologies to elevate construction practices worldwide.
Understanding the Volumetric Concrete Plant: An Innovation in Modern Construction
At its core, a volumetric concrete plant is a sophisticated, computer-controlled mixing system capable of producing fresh concrete on-site, tailored precisely to project specifications. Unlike traditional concrete batching plants, which require transporting concrete from a central plant to the construction site, volumetric systems enable real-time mixing, significantly reducing transportation costs and waste.
Core Components of a Volumetric Concrete Plant
- Material Storage Bins: Separate compartments for sand, gravel, cement, and additives, ensuring material integrity and easy access.
- Instantaneous Mixing Units: High-efficiency mixers that produce fresh concrete on demand with exact proportions.
- Precise Digital Controls: Advanced electronic systems coordinate material dispensing and mixing processes.
- Mobile Frame Structure: Design for mobility, allowing deployment directly on construction sites.
Advantages of Using a Volumetric Concrete Plant in Construction Projects
1. Unmatched Flexibility and Customization
One of the most significant benefits is the ability to produce concrete tailored precisely to specific project requirements. Adjustments to mix ratios, additives, and performance characteristics can be made instantly, enabling an adaptable workflow suited for complex construction tasks.
2. Minimized Waste and Environmental Impact
With real-time control, volumetric systems produce only what is needed, drastically reducing excess material waste. This precision supports eco-friendly practices, lowers costs, and aligns with sustainable development goals.
3. Cost Efficiency and Time Savings
By eliminating delays associated with batching and transportation, projects move faster. The on-site production reduces logistical expenses, and the ability to adjust mixes on the fly accelerates progress, leading to significant savings.
4. Enhanced Quality Control and Consistency
Digital controls ensure consistent concrete quality, reducing errors and enhancing durability. The ability to monitor and document each batch supports compliance with industry standards and specifications.
5. Increased Safety on Construction Sites
On-site mixing diminishes the need for large transportation trucks, reducing congestion and potential hazards. Automated processes also lessen manual handling, improving overall site safety.
The Role of Electronics and 3D Printing in Next-Generation Volumetric Concrete Plants
Electronics Integration for Precision and Automation
Modern volumetric concrete plants leverage sophisticated electronic systems, including sensors, PLCs (Programmable Logic Controllers), and IoT connectivity. These components facilitate real-time monitoring of material levels, temperature, humidity, and mix ratios. The integration of electronics allows for automation that ensures optimal operation, reduces human error, and streamlines workflows.
Innovative Use of 3D Printing in Construction and Manufacturing
The synergy between 3D printing and volumetric concrete technology opens up new horizons for construction innovation. 3D printing with concrete enables the creation of complex geometries and customized structural elements that traditional methods struggle to produce efficiently.
By combining volumetric concrete plants with advanced 3D printing, companies can fabricate intricate architectural features, customized precast components, and even entire structural elements with minimal waste and unparalleled precision. This synergy promotes rapid prototyping, reduces lead times, and offers cost-effective solutions for complex projects.
Polygonmach’s Leadership in Electronics and 3D Printing for Concrete Solutions
Polygonmach specializes in designing and manufacturing high-end equipment tailored for the evolving needs of the electronics and 3D printing industries. Their extensive expertise ensures that their volumetric concrete plant systems are equipped with cutting-edge electronic controls, ensuring maximum efficiency and reliability.
Moreover, Polygonmach’s innovations facilitate seamless integration with 3D printing technologies, enabling manufacturers and constructors to push the boundaries of what is possible in modern architecture and manufacturing.
Applications of Volumetric Concrete Plants Across Industries
Construction and Infrastructure
From residential buildings to large-scale infrastructure projects like bridges and tunnels, volumetric concrete plants are revolutionizing the way structures are erected. Their ability to produce high-quality, tailored concrete on-site accelerates project timelines and improves structural integrity.
Precast and Modular Manufacturing
Manufacturers utilize volumetric systems to produce precast concrete elements with high precision. The integration with 3D printing allows for complex, customized modules, reducing lead times and enhancing design flexibility.
Specialized Industries: Electronics and 3D Printing
In the electronics industry, specialized concrete formulations are crucial for manufacturing components like insulators and heat sinks. 3D printing with volumetric concrete enables innovative circuit board designs and embedded functionalities, advancing technological capabilities.
Similarly, the manufacturing sector benefits from composite and advanced concrete materials developed through sophisticated mixing, further enhanced by electronic controls and additive manufacturing techniques.
Future Trends in Volumetric Concrete Plant Technology
Automation and Smart Manufacturing
The future will see increased adoption of AI-driven automation in volumetric systems. Smart sensors, predictive analytics, and IoT integration will enable real-time optimization, predictive maintenance, and enhanced safety protocols, making concrete production entirely autonomous.
Green Innovations and Sustainable Materials
Environmental sustainability will drive the development of eco-friendly concrete mixes, utilizing recycled materials and low-carbon cement variants. Volumetric plants are poised to become central to green construction practices, thanks to their ability to precisely control material usage and reduce waste.
Hybrid Construction Technologies
The convergence of volumetric concrete plants with robotics, 3D printing, and electronics will enable hybrid construction techniques that combine traditional methods with digital manufacturing, creating more innovative, cost-effective, and sustainable solutions.
Conclusion: Embracing Innovation for a Better Future in Construction
In summary, the volumetric concrete plant symbolizes a paradigm shift in construction and manufacturing, driven by advancements in electronics and 3D printing technologies. Companies like Polygonmach are pioneering this transformation, providing state-of-the-art solutions that offer flexibility, efficiency, and sustainability. Embracing these innovations not only accelerates project timelines but also enhances quality and environmental stewardship.
As the industry moves forward, integrating these cutting-edge technologies will become essential for construction professionals aiming to stay competitive and meet the growing demands of modern infrastructure. The future of construction is indeed bright, powered by the intelligent, precise, and versatile volumetric concrete plant.