Understanding the Importance of Silicone Membrane for Vacuum Press
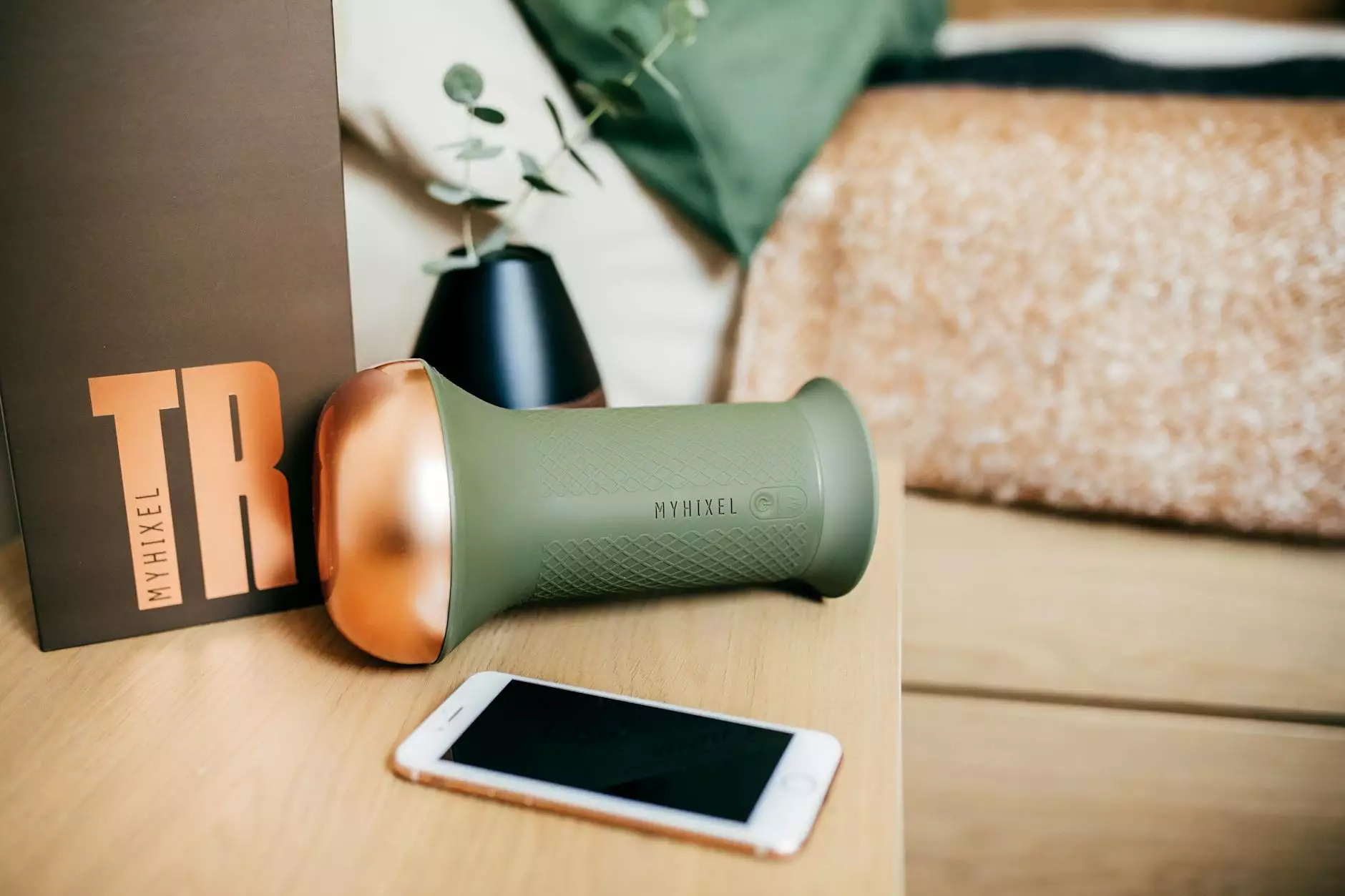
Silicone membranes for vacuum presses are essential components in various industries, including woodworking, composites, and the production of packaging materials. Utilizing such membranes can significantly improve the quality and efficiency of your vacuum pressing operations. In this article, we delve into why silicone membranes are favored by professionals, their advantages, and how to choose the right one for your business needs.
What is a Silicone Membrane?
A silicone membrane is a flexible and durable material, typically used in vacuum pressing applications to provide a reliable sealing surface. Made from high-quality silicone rubber, these membranes exhibit excellent elasticity, temperature resistance, and chemical stability.
Types of Silicone Membranes
Silicone membranes can be classified into several types based on their thickness, durability, and specific applications:
- General-purpose Silicone Membranes: Ideal for most vacuum pressing applications.
- High-temperature Silicone Membranes: Suitable for processes with elevated temperatures.
- Specialized Silicone Membranes: Designed for particular industries, such as aerospace or food processing.
Benefits of Using Silicone Membranes
Incorporating silicone membranes into your vacuum press system offers numerous advantages:
- Temperature Resistance: Silicone membranes can withstand high temperatures without losing integrity, making them ideal for various materials.
- Durability: These membranes exhibit exceptional wear and tear resistance, ensuring a longer lifespan compared to traditional rubber membranes.
- Chemical Resistance: Silicone's innate stability allows it to resist chemicals and solvents that may be encountered in industrial applications.
- Flexibility: The flexibility of silicone allows for easy application over uneven surfaces, ensuring consistent pressure during the vacuum process.
Applications of Silicone Membranes in the Industry
Silicone membranes find applications across various sectors. Here are some prominent uses:
1. Woodworking Industry
In woodworking, silicone membranes are employed for veneering and laminating processes. Their ability to form a tight seal ensures optimal adhesion and a perfect finish.
2. Composite Manufacturing
Silicone membranes play a vital role in the composite materials industry, especially for processes like resin infusion. The flexibility and chemical resistance enhance production efficiency and product quality.
3. Packaging Industry
In packaging, silicone membranes are utilized for vacuum sealing products. Their durability and ability to create an airtight seal protect goods from environmental factors.
Why Choose a Silicone Membrane for Your Vacuum Press?
When considering what type of membrane to incorporate into your vacuum press, silicone membranes stand out due to their numerous advantages:
- Long Service Life: The durability of silicone membranes leads to reduced replacement frequency, ultimately saving costs.
- Enhanced Performance: The superior sealing properties provide better vacuum conditions compared to rubber membranes.
- Cost-Effectiveness: While the initial investment may be higher, the longevity and efficiency improvements make silicone a worthwhile choice.
How to Choose the Right Silicone Membrane
Selecting the appropriate silicone membrane for your vacuum press involves several considerations:
1. Determine Your Application Needs
Identify the specific requirements of your application, such as the type of materials, required temperature resistance, and pressure levels.
2. Assess Thickness and Size
The thickness and size of the silicone membrane should align with the specifications of your vacuum press. Ensure that the chosen membrane fits securely without excess slack.
3. Evaluate Compatibility
Consider the materials you will be vacuum pressing. Ensure that the silicone membrane is compatible with the substances to avoid degradation.
Purchasing Silicone Membranes for Your Business
When it comes to buying silicone membranes, vacuum-presses.com offers a range of high-quality options. Here’s what to consider:
1. Trusted Suppliers
Always purchase from reputable suppliers. Look for manufacturers that have a strong track record and positive customer feedback.
2. Variety of Options
Choose suppliers that offer a diverse selection of silicone membranes, including different thicknesses and grades. This ensures you can find the perfect membrane for your needs.
3. Custom Solutions
Some suppliers may offer custom solutions tailored to specific applications. Don’t hesitate to inquire about custom sizes or special features if needed.
Silicone Membrane Care and Maintenance
To maximize the lifespan and performance of your silicone membrane, implement a proper care and maintenance routine:
1. Regular Cleaning
Ensure that the membranes are cleaned regularly to remove dust, residue, and debris. Use mild cleaning agents compatible with silicone.
2. Inspection for Wear
Periodically inspect the silicone membranes for signs of wear or damage. Promptly replace any compromised membranes to maintain vacuum quality.
3. Proper Storage
When not in use, store silicone membranes in a cool, dry environment away from direct sunlight to prevent degradation.
Conclusion
In conclusion, the use of a silicone membrane for vacuum press applications is a decision that can greatly enhance the productivity and quality of your manufacturing processes. By understanding the benefits, applications, and maintenance practices, you can make informed choices that will benefit your business in the long run. For exceptional quality silicone membranes, visit vacuum-presses.com today and elevate your vacuum pressing operations.
© 2023 Vacuum Presses. All rights reserved.